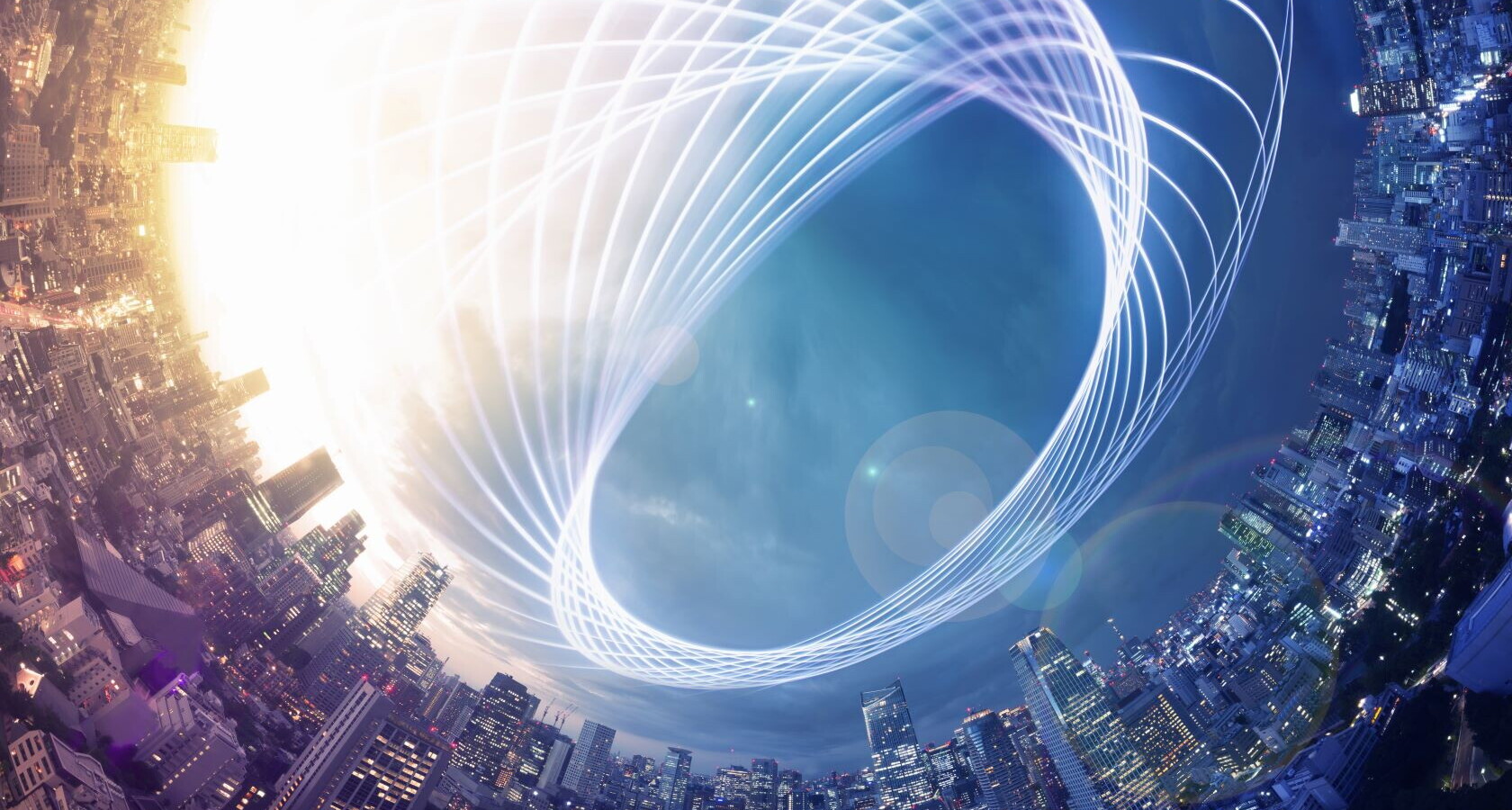
Industry for the Transition, Opportunities and Perspectives
In the spotlight
CCS is an indispensable technology for decarbonizing the highest emitting industries. Regardless of the obstacles, one thing is clear: we need to integrate this technology.
12 minOften the fight against climate change has become synonymous with the need for increased clean energy deployment. Yet despite remarkable advancements in clean energy generation over the past decades, and the use of that energy to decarbonize sectors where electricity is a major input, the reality is that some sectors of industry remain difficult to abate. Still a poorly defined concept, ‘hard-to-abate’ broadly refers to sectors where electrification and energy efficiency enhancements are not viable or sufficient decarbonization options – whether technically or financially, or both – and where deep decarbonization is needed if we are to achieve true net-zero.
These include heavy industries such as iron & steel, cement, and chemical production, as well as aviation and shipping, collectively accounting for ~30 percent of global CO2 emissions. Iron & steel and cement production contribute around 2/3 of these emissions alone (i.e. 20 percent globally), as both processes require very high temperatures from fuel combustion which cannot be easily produced with electricity. For these sectors, efforts to lower CO2 emissions can take a few forms: lowering demand and enhancing recycling rates, substituting the use of fossil fuels with alternative clean fuels such as (green) hydrogen, or capturing and ridding of CO2 through carbon capture and storage (CCS).
In cement production specifically, CO2 emissions are intrinsic to the process itself (70 percent are ‘process emissions’) which cannot be otherwise mitigated with clean electricity and where CCS is not only an option, but a necessity. In effect, around 30 CCS cement projects are currently in different stages of development globally, mostly in Europe. In parallel, the cement industry continues to pursue the production and use of alternative, innovative low-carbon input materials, yet it is becoming increasingly clear that CCS will play a leading role in decarbonizing the sector, at least in the short-to-medium term.
This contrasts with the steel industry where CCS is not expected to feature as heavily – at least not directly. This is despite more than half of global steel production coming from China, where most production (>80 percent) uses coal-based blast furnaces which can only be decarbonized through CCS or by switching to cleaner input materials. The fact that there are different CO2 emission point sources in the steelmaking process means that CCS needs to be selectively deployed at the highest emitting point (the blast furnace) which, at best, achieves 50-60 percent reduction in overall emissions. In addition, common to both steel and cement production, CO2 concentrations in flu gases are relatively low (10-30 percent) which means that capture processes would consume more energy and require larger equipment. This cost barrier, and a lack of adequate policy support, is the reason why there are very few full-scale CCS projects operating in heavy industry today, mostly tacking the relatively concentrated CO2 emitted during hydrogen production in oil refineries.
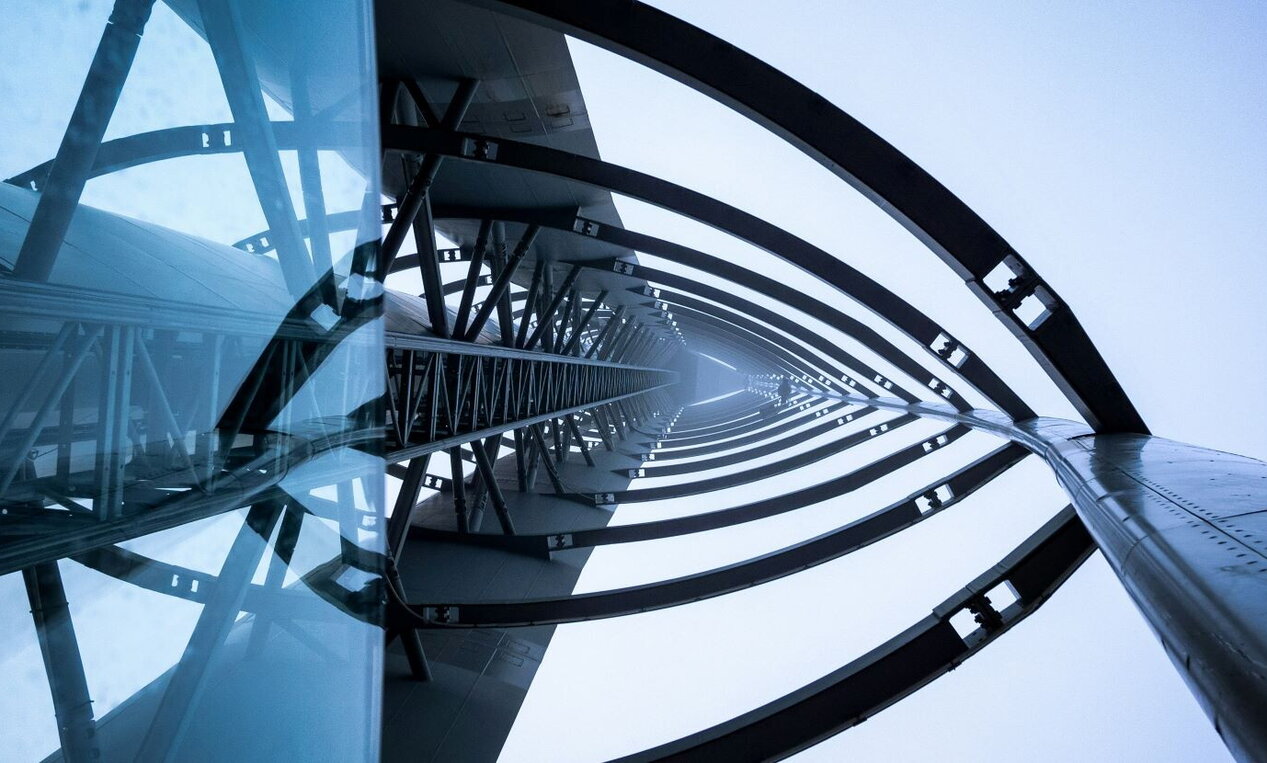
That said, CCS has potential to play an indirect role in decarbonizing iron & steel. Most announced ‘green steel’ projects rely on the use of hydrogen to directly reduce iron (DRI) – instead of coke in blast furnaces – coupled with electric arc furnaces that then transform iron into steel. If both processes (i.e. the production of hydrogen through electrolysis and operation of the arc furnace) are powered via clean electricity, the steelmaking process becomes effectively carbon-free. Yet, green hydrogen use in steelmaking is still a nascent practice and is prohibitively expensive without strong policy support, and one that may well be limited to areas with cheap clean electricity and rich iron ores (e.g. Brazil, Australia). This is where CCS comes in: by decarbonizing natural gas or hydrogen (‘blue’ hydrogen) before its use for iron reduction, CCS can provide a decarbonization solution for steelmakers in regions where renewables may not be abundant and/or where suitable conditions already exist for CCS deployment (e.g., the right geology for carbon storage, cheap natural gas prices). To that extent, CCS can play an intermediary role in decarbonizing DRI-based steel plants, until such time when green hydrogen becomes a more financially viable solution (as electrolyser costs depreciate).
Cost an impediment, still
CCS is a technology that, by definition, has no intrinsic economic value – assuming CO2 is not utilized for commercial purposes – other the environmental virtues associated with carbon avoidance. In that sense, as opposed to decarbonization solutions such as renewable energies or clean hydrogen which offer tangible and tradeable products, CCS is merely a (waste management) service. The widely-cited lack of financial revenue from CCS remains the largest barrier to deployment but one that can be more relevant in certain regions and/or sectors than others. For instance, in the US where carbon capture has been demonstrated for decades, the technology’s deployment was historically driven by its capacity to stimulate existing oil fields to produce more oil through enhanced oil recovery (EOR). To alleviate the financial burden in absence of utilization outlets, a combination of support mechanisms will be needed. This is perhaps best demonstrated using the technology’s status quo in Europe as an example.
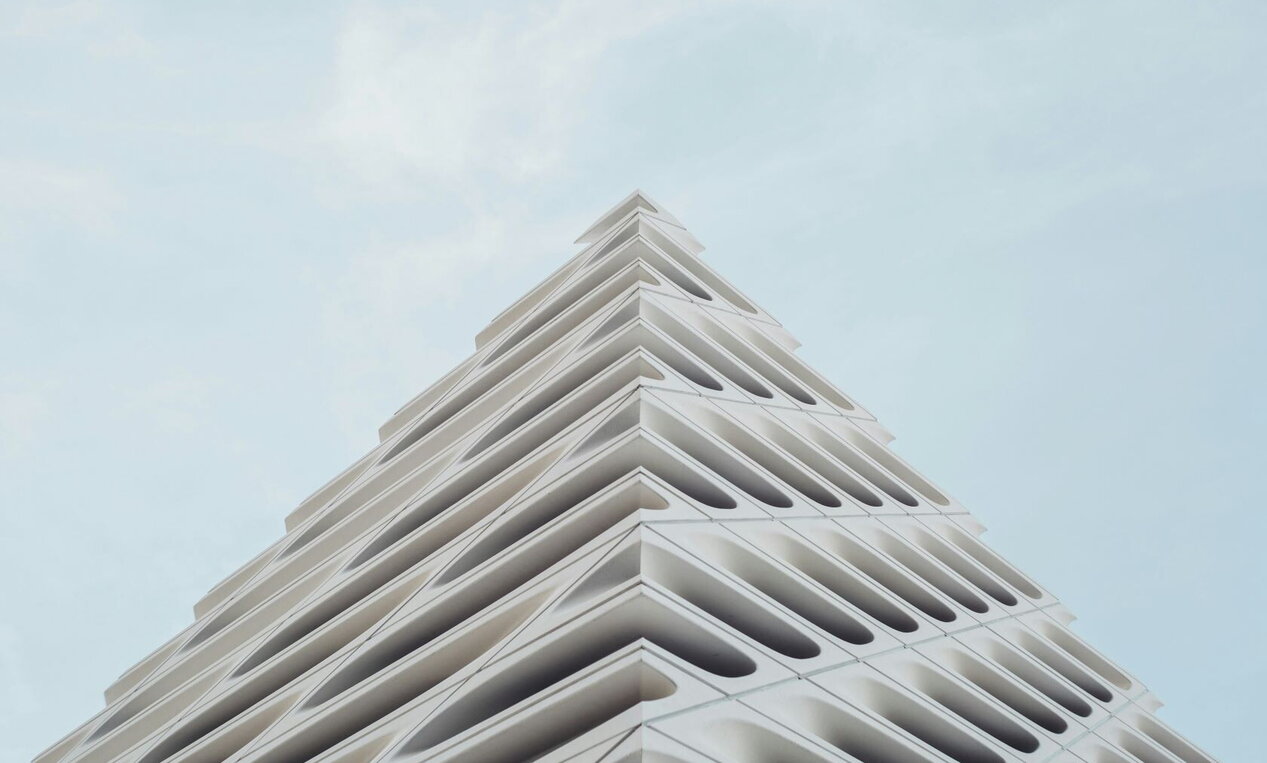
Within the scope of the EU Emissions Trading System (EU-ETS), most sectors which exhibit the highest potential for CCS deployment (e.g., power sector, oil refineries, cement, iron and steel) are included. Here, operators can use CCS to capture and permanently store CO2 and in turn claim equivalent reductions in compliance costs (i.e., fewer allowances need to be purchased). However, despite EU carbon prices recently reaching record-highs of around €100/tCO2, they remain insufficient to incentivize deployment and no current European CCS project is fully supported by the EU carbon price.
To address this mismatch, jurisdictions such as the Netherlands have introduced a Carbon Contracts for Difference (CCfD) mechanism to top up support provided under the EU-ETS. Simply put, a CCfD subsidizes the price differential between the allowance price (‘reference’ price) and actual costs of CCS (the CO2 abatement cost). From an operator’s perspective, this hedges against the risk of fluctuating carbon prices and should in turn create higher investor confidence in the long-term financial performance of the technology. Other non-market mechanisms can also support this: in the EU, the recently announced Net Zero Industrial Act sets an annual target of 50Mt storage capacity by 2030 on a continental-level, which complements the aforementioned (capture-targeted) schemes. In the UK, a similar CCfD-type mechanism – the Industrial Carbon Capture (ICC) contracts – is based on carbon pricing and provides industrial emitters with an incentive to capture CO2. In the US, a subsidy per ton of CO2 captured and stored is paid to adopters under a direct-pay model (in the form of 45Q tax credits), while investment tax credits are at the base of the CCS business model in Canada.
Who pays in absence of sufficient public support?
As far as hard-to-abate industrial sectors are concerned, unless strong and protective policy measures are in place, adopting CCS would explicitly put an operator at a market disadvantage especially if costs were to be passed down to end-users. In the case of cement, steel and chemical production, this translates to higher material costs. Early cost projections show that CCS would increase production costs by at least 20-30 percent for ‘green steel’ and 60-70 percent for cement. As these commodities are traded globally and in highly-competitive markets, a small increase in price would mean market share loses for green producers as consumers opt to switch to cheaper (‘browner’) suppliers. Here, measures such as carbon border adjustments can in theory protect against such carbon leakage; however, these are yet to be implemented and their effectiveness assessed in practice.
On the bright side, deploying clean technologies such as CCS in hard-to-abate material industries has an advantageous feature that is distinct from that of clean solutions in the power sector (be it CCS on fossil-fuelled plants, or renewable energies) – and that is product traceability. As opposed to clean energies which feed into a single grid and are effectively untraceable to their sources, green materials can be traced to specific manufacturers, where appropriate certification and standards setting can create demand for the green products. This also means that support for CCS does not need to be targeted at the project level only but can also start with final consumers.
Examples of demand-side ‘pull’ mechanisms can include green public procurement and regulatory mandates on large material consumers (e.g. construction and automotive companies) to integrate green materials into production lines. These can help drive demand and in turn incentivize clean technology adoption such as CCS. Targeting downstream use of the green products also means that the significant increases in steel and cement costs which were noted earlier can translate to negligible premiums on the final products: for instance, a vehicle’s cost increases by less than 1 percent if made with green steel as does the construction of a bridge if made with greener steel and cement. The question then becomes: is there willingness by the manufacturer and its end-customer to pay that premium?
A question of ‘how’ and ‘when’
A recent trend of voluntary demand from the automotive and construction industries for greener materials says ‘yes’. Car manufacturers are especially interested in procuring greener steels as one way of mitigating their Scope 3 emissions. Manufacturers are also anticipating regulatory changes that could pose potential threats to their business models (e.g. introduction of CBAM and phasing out of free allowances under the EU-ETS). At the estimated premium, procuring green materials may be cheaper than paying carbon prices which are only expected to increase in time. That said, voluntary demand on its own will not suffice to deploy CCS at the scale needed to make meaningful climate contributions, and a combination of the above measures will certainly be needed. Yet, despite the barriers, one thing is clear and that is for the highest-emitting and hardest-to-abate sectors integrating CCS is not a question of whether, but of how and when?